激光切割自动上下料加钣金料库的优势?
激光切割诞生于20世纪70年代,切割源主要有CO2、光纤激光器,其工作原理主要为激光器输出高能量密度的激光束聚集在工件的表面上,使工件上被超细焦点照射的区域瞬间熔化和气化,同时用与激光束同轴的压缩气体吹走被熔化材料,通过数控机械系统移动光斑照射位置而实现自动切割,形成一定形状的切缝。设备主要由激光器、机床、数控、冷水机、冷干机、空压机等构成。其发展方向为低成本、高功率、大幅面、高效率、高精度和高智能化。
在激光切割机的使用过程中,人工上下料产生了效率低和劳动强度大的问题。同时排版不规范,未充分利用板幅也造成了原材料的浪费。随着激光的广泛应用,这些问题开始日益突出和明显。介绍自动上下料对效率和劳动强度的影响,以及集中排版对材料利用率带来的提升。
传统的激光设备供料方式为单台设备分散供料,上下料效率低。钢板存放方式为钢板散放,上料方式为人工吸盘上板,下料方式为每台激光设备加工完成后各自进行人工分拣。任务处理方式为激光加工时进行N+1任务排版编程,人工U盘拷贝到激光设备,启动。
- 钢板存放
上料
下料
其主要存在以下三点问题:
(1)上板时人工吊板,效率低。
(2)钢板多小片散放,占用场地多。
(3) 2人排版/4台,4人分拣/4台,占用人员多。
引进立体料库和自动化输送系统,联网激光切割机,为多台激光设备自动集中配料,可形成以设备为主体的自动化流水线,实现激光自动上下料少人化直至无人化运行。可以实现物料集中分拣,提高上下料效率。钢板存放方式为立体存放,信息输入数据库。上料方式为上料移载机自动上板。下料方式为下料移载机将已加工整板物料搬运到分拣台进行人工集中分拣。任务处理方式为集中排版编程,程序放入控制系统进行自动分配,人工干预调整。
整套设备主要由自动立体料库,激光切割机,编程控制单元,吸盘上料装置,料叉下料装置,成品分拣台组成,可实现从编程到原材料存储,原材料上料,切割,切割后工件以及废料的搬送,实现自动化和按计划运转,提高生产效率,节省操作人员,降低劳动强度,节约场地。
- 自动立体料库
- 吸盘上料装置
- 料叉下料装置
实现从编程到原材料存储
其主要有以下八大优势:
(1)自动上板,提高效率。
(2)钢板分层存放在料库,节约场地。
(3)系统集中排版、控制,集中分拣,1人排版/4台,2人分拣/4台,可以发挥人员集中的优势。
(4)实现自动化操作,提高机床利用率。
(5)不同厚度材料智能分层管理,较小的面积,提高空间使用率。
(6)可随时进行拓展,实现多台机器共线生产,提高生产能力。
(7)降低劳动强度,减少操作人员,安全高效。
(8)自动化程度高,提升公司品牌形象。
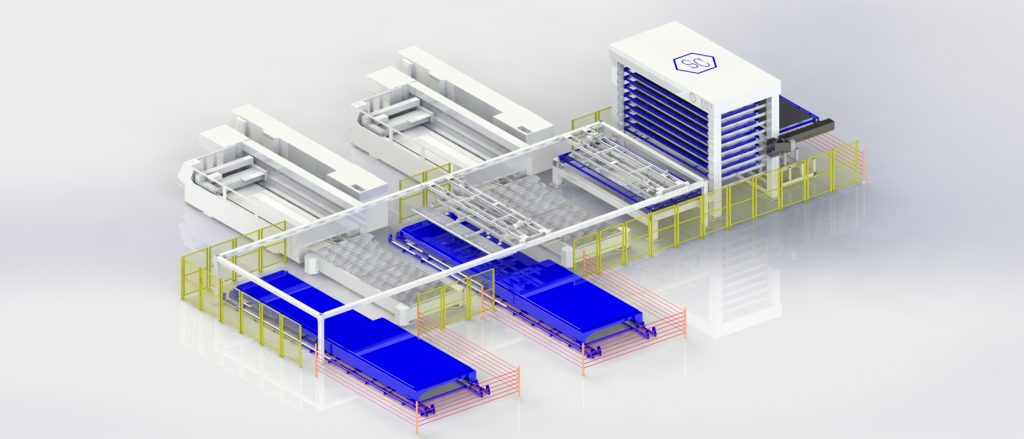
- 对比分析
下面从三个方面对此系统应用前后进行对比分析:
优劣势对比分析
配备立体自动化料库,可进一步实现自动上下料,提高上板效率,减少操作人员,降低劳动强度,节约场地。经综合分析,以一拖三为例,上板效率可提升78%,同时可节省操作人员及场地,有效降低劳动强度,改善员工工作环境。
(1)工艺对比。
旧工艺:钢板散放,激光机布局分散、工作台与绿色通道平行;人工分批次多次编程,分配到每台设备进行加工,人工上板,人工下料。
新工艺:钢板分层存储在立体料库中,激光机集中布置、工作台与绿色通道垂直;人工编程后批量导入工控机以及激光主机,具有智能化的控制系统,自动分配任务,通过激光主机与上下料系统配套工作,实现“料库预上料—吸盘吸料—上料—交换工作台—切割—交换工作台—下料”的全自动循环运行,可以自动,切割循环自动进行,也可选择手动,只完成一个切割循环。
(2)人员、效率对比。
旧工艺:编程(分批次多次处理)—人工为每台激光机分配任务—拷贝切割程序到激光机—人工吊板—对中—人工交换工作台—启动切割—人工交换工作台—成品料人工分拣。
效率:旧工艺上板、对中效率低,实际测算上板以及对中时间总和约为5min。
新工艺:集中编程—将当日所有待加工任务导入工控机—任务自动分配—上料移载机自动上板—自动交换工作台—启动切割—自动交换工作台—下料移载机将成品料叉到分拣台—人工分拣。
效率:使用立体自动化料库平均上板时间为1.1min(3台上板共需要200s)。
(3)占地面积对比。
旧工艺:钢板散放,激光机布局分散且工作台与绿色通道平行。如采用与前期通快激光机相同的布置方式,单台激光机占地约104m2(长11.25m,宽9.25m),3台激光机需占地:104×3=312m2;为满足钢板不同料厚和材质的存放需求,钢板实际存放占地104m2(长11.25m,宽9.25m)。
则共需场地:312+104=416m2。
新工艺:钢板分层存储在立体料库中,激光工作台与绿色通道垂直。整套生产线占地面积:30m×9.25m=277.5m2。
新工艺相比于旧工艺可以节省场地:416-277.5=138.5m2。
(4)劳动强度对比。
1)旧工艺人工上板、对中,劳动强度大,新工艺自动上板、对中,劳动强度小。
2)旧工艺在激光机工作台上分拣,必须多人作业及时分拣完,否则影响激光机正常工作,新工艺将成品料全部转移到分拣台上分拣,可以单张也可以多张分拣,灵活性高。
3)新工艺自动化程度高,员工作业环境好。
控制过程及工艺流程
工艺流程如下:
1)具有智能化的控制系统,激光主机与上下料系统配套工作,能实现“上料台预上料—吸盘吸料—校正平台校正板料—吸盘上料—交换工作台—寻边—切割—交换工作台—下料至分拣区”的全自动循环运行,可以选择自动模式,切割循环自动进行,也可选择离线模式,只完成一个切割循环。
2)当自动上下料系统出现故障时,支持手动上下料,且激光主机配合产线任务指派软件仍可以实现单机“交换工作台—寻边—切割—交换工作台”的单循环自动运行。
3)产线任务指派软件将排版生成的加工程序按料厚进行分组排序并生成一个任务单,导入到控制系统时能自动读取料厚等相关信息。任务单导入后,控制系统给激光机自动分配任务,并根据激光机的运行情况进行实时调整。
4)产线监控管理系统可以记录激光切割机的工作信息,导出生产报表,报表包括以下内容:板材信息、切割程序物料号、物料数量、开始时间、结束时间、切割时间、设备使用率等,可实时监控管理整条生产线。
5)料库能自动识别所切割程序对应的板材材质、厚度等信息,切割时能自动选择料库中的板料,程序材质切换时,系统可自动完成料库中的板料切换。
6)料库根据控制系统的程序分配,自动提前准备下一道程序所需要的钢板并将其放在预上料工作台上。
7)料库可根据当前加载的加工单进行自检,缺板时发出提醒,由人工进行补齐。
8)料库能自动识别切割程序所对应的板材材质、厚度等信息,切割时能自动选择料库中的板料。板材在切换时,系统可自动完成料库中的板料切换。人工每向料库中补一次原材料,可通过操作界面将所补原材料信息维护进系统中。
9)加工过程中生产任务删除,增加或者根据紧急情况前后调整以及设备出现异常问题时,产线任务指派软件无需人工干预可进行自动调配,设备功能恢复后,仍按正常时进行分配。
10)首次开机加工时,可以自动检测激光机工作台上是否存在板料,根据实际情况按效率最大化的原则开始上板加工。
11)自动分配任务时可避免集中上板,集中下料的情况出现。
12)整套流水线节拍合理,保证设备利用最大化,不会出现待机现象。
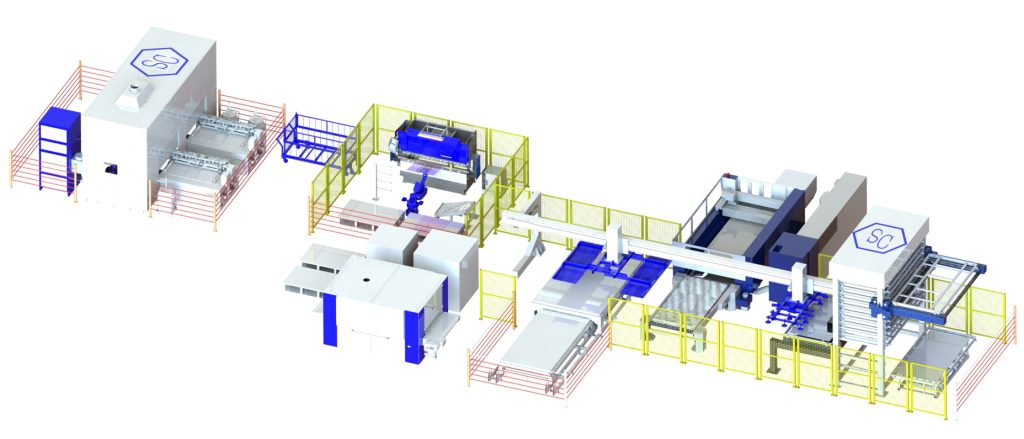
- 经验教训
通过对激光机料库自动上下料的研究和探索,总结经验教训,关键点如下:
(1)信息交互问题。
料库与激光切割机最好能够实现信息的实时交互,也就意味着激光切割机的控制系统要向料库的控制系统开放端口及信号。具体为:
1)前提:提供上位软件和机床的通讯接口。
2)提供机床状态信号(切割运行中、切割准备好、报警)。
3)提供机床工作台交换准备好信号、工作台交换的启动信号以及工作台交换的完成信号。
4)提供机床切割程序的启动信号及切割已完成信号。
5)机床能够接收上位软件发送给机床的程序,自动调用对应加工材料的切割工艺参数,并且当上位发送给机床切割程序启动信号后,机床可以调用相应的切割程序进行切割。如部分信号确实无法开放,则会限制以上交互的实现。
(2)激光剑栅与下料料叉匹配问题。
下料装置为料叉下料,下料过程中既不能出现成品料掉落的问题,也不能出现由于熔渣将激光工作台一同叉起的情况,这就对激光切割机工作台的制造及安装精度以及料叉的设计提出了更高的要求。下料机料叉间距要与激光剑栅间距匹配,要考虑激光剑栅尺寸误差的风险应对措施。
其他需要注意的事项如下:
(3)自动生产线的长,宽,高,间距要与现场匹配,布局要与要求一致。
(4)自动生产线主体结构强度分析过程,要与板材的重量相匹配。
(5)料库层数,料库托盘尺寸,补板平台尺寸要与原材料数量,尺寸匹配。
(6)对正平台要能实现钢板对齐的功能。
(7)上料机吸盘分张,断电保护措施要具备。
(8)上料机布置位置要合理,要方便上料。
(9)下料机料叉结构强度要与板材特点相匹配,要考虑长时间工作后是否变形,如变形如何应对。
(10)分拣台大小数量要足够。
(11)要具有临时上下板措施。
(12)整套设备布局要合理,操作方便性要充分考虑。
(13)自动生产线运行过程和逻辑要合理。
(14)整套生产线安全防护措施要到位。
(15)生产线各过程时间,节拍要协调有序,要与切割时间相匹配,不能有明显的等待现象。
(16)要考虑噪声,噪声如不达标,要采取相应的降噪措施。
(17)尽量配备格栅清理机,防止割渣影响下料。
总之,通过激光切割机上下料系统的应用,可显著提高生产效率,降低操作人员劳动强度,节省设备占用场地,是后续钣金加工设备自动化、智能化的发展方向。